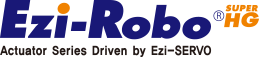
- 1. Hollow Rotary Table
-
Large Diameter hollow bore to penetrate the output table equipped SHG Series ensure flexibility and convenience in the design of equipment when install complex wiring and piping.
-
Model Name |
Size of plinth(Frame Size) |
Hollow Bore Diameter |
SHG130 |
130mm |
Ø56mm |
SHG170 |
170mm |
Ø85mm |
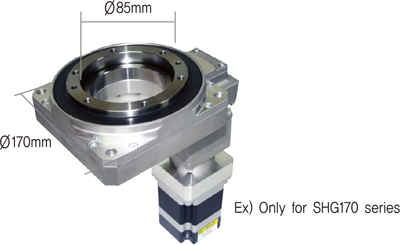
- 2. Accurate Gear Driven
-
Since it is directly driven by a gear with extremely low backlash, the repeatability of positioning in one direction is ± 15sec, Lost Motion by positioning in both directions is less than 2min. Therefore precision positioning is possible. Unlike belt pulley systems, maintenance costs are reduced because little maintenance is required, such as adjusting the belt tension.
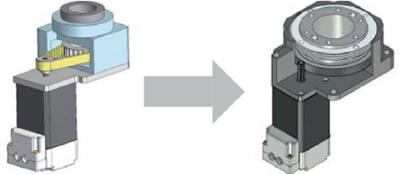
- 3. High Reduction Ratio & High Torque
-
Super HG Series offers high gear ratio as 1:20, 1:36 for model SHG170 and 1:18 for model SHG130 so it enables to drive high inertia of load with very strong output torque from hollow rotary table. Also high gear ratio enables minimization of load inertia moment ratio so it realizes smooth operation at Acceleration/Deceleration and no hunting when it stops suddenly.
-
Model |
Gear Ratio |
Gear Level |
SHG130 |
18 |
2nd Stage Gear |
SHG170 |
20, 36 |
2nd Stage Gear |
※ High gear ratio enables high torque output and operation of high inertia of load.
- 4. High Rigidity
-
High rigidity of cross Roller Bearing and hollow rotary table integrated SHG Series maximizes rigidity of Actuator to support all directions of load as radial load, thrust load and moment load.
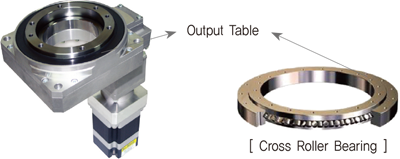
- 4. Fast Response
-
Similar to conventional stepping motors, Ezi-SERVO instantly synchronizes with command pulses providing fast positional response. Ezi-SERVO is the optimum choice when zero-speed stability and rapid motions within a short distance are required. Traditional servo motor systems have a natural delay between the commanding input signals and the resultant motion because of the constant monitoring of the current position, necessitating in a waiting time until it settles, called settling time.
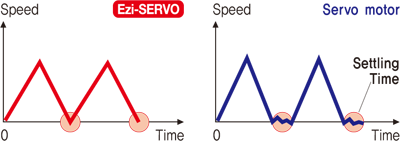
- 6. Supporting Various Field Network Solutions
-
By matching with Ezi-SERVO, Closed Loop Stepping System, Ezi-ROBO SHG could be connected with the master controller such as PC/PLC though vaious field networks such as EtherCAT, Ethernet, RS-485, CCLink and so on. In case of controller embedded products such as Ezi-SERVO Plus E and Plus R, motion library (DLL) for Windows XP/7/8/10 can be provided.
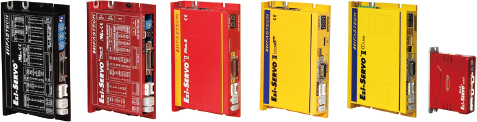
- 7. Applicable to Abrupt Load Fluctuations and Rapid Acceleration Applications
-
The Ezi-Robo SHG Series driven by Ezi-SERVO, a closed-loop stepping motor control system without step-out, has no fine vibrations, i.e. hunting problem unlike general servo system. In addition, It is Tuning Free Actuator that does not require gain adjustment for abrupt load fluctuation.
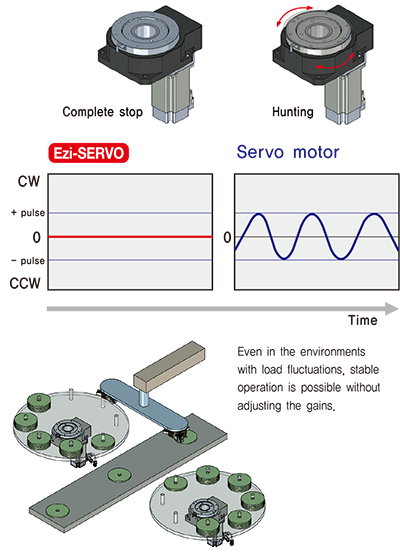
- 8. Variety of Input/Output Signals and User Setting Function
-
Nine Input port and nine output port can be defined with various functions by user. Therefore, It provides flexibility and can saves effort to change wiring.
- 9. Position Table Function
-
Position Table can be used for motion control by digital input and output signals of host controller. You can operate the motor directly by sending the position table number, start / stop, origin search and other digital input values from a PLC. The PLC can monitor The In-Position, origin search, moving / stop, servo ready and other digital output signals from a drive. A maximum of 256 positioning points can be set from PLC.
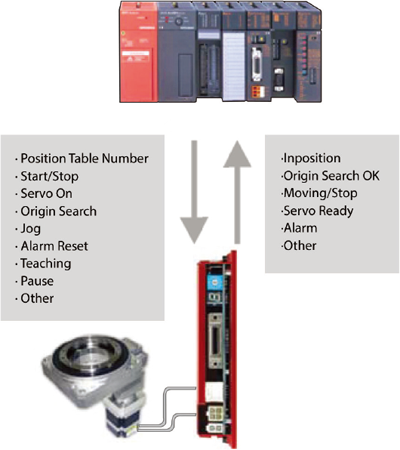
- 10. Examples of Ezi-Robo SHG Applications
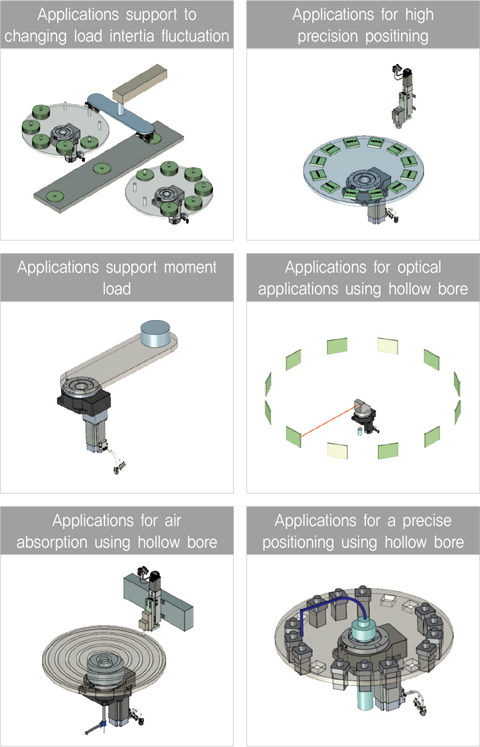